Defeating Glaze Pinholing and Pitting: Secrets to Perfect Ceramic Finishes
Pinholes and pits in fired glaze surfaces are common ceramic defects that can affect the quality of pottery. Pinholes are small holes that penetrate down to the body below, while pits are smaller and mar the surface without penetrating all the way down. These imperfections, often no larger than the head of a pin, are a result of gases generated during firing that need to escape through the glaze melt.
Effective control of glaze pinholing and pitting requires understanding their causes and implementing precise adjustments in glaze composition and firing techniques. Larger pinholes may sometimes be mistaken for crawling. In pottery production, addressing issues like glaze pinholes and pitting involves various strategies such as adjusting firing techniques, glaze application, and glaze composition to ensure a flawless final product.
Causes of Glaze Pinholing and Pitting
Pinholes are often caused by gases generated during firing, associated with the decomposition of organic materials and minerals, which need to escape through the glaze melt. Factors like firing speed, glaze composition, and body out-gassing contribute to the formation of pinholes.
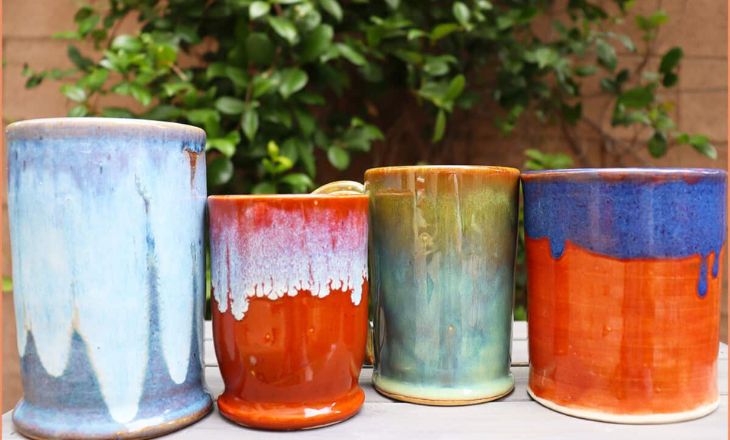
Factors Affecting Pinholes
The type of clay used, construction methods, glaze application, and firing schedules can all influence the appearance of pinholes in pottery glazes. Thicker walls, rough surfaces from trimming, and the size of the pottery pieces can impact the likelihood of pinholing.
Pinholing in ceramics can be minimized by meticulous glaze application and controlled firing processes, ensuring smooth and defect-free surfaces. By implementing various strategies and considering factors like clay type, construction methods, and firing schedules, artists can minimize the occurrence of these common glaze defects.
Are Large Particles or Gas-Producing Materials Present?
A sieve analysis of the body is essential to identify the presence of large particles. After weighing, firing the sample to cone 04, and re-weighing any significant weight loss indicates decomposition and gas generation. Volatile particles like lignite or sulfur compounds can produce high gas volumes, overwhelming the glaze’s self-healing ability.
To avoid this, remove these materials from the body batch in favor of finer particles to distribute gas generation more evenly. Opt for cleaner alternatives such as low-lignite and low-sulfur ball clays to mitigate gas-related issues effectively.
Are the Particles Melting Vigorously?
To investigate if coarse particles in the clay body are contributing to pinholing issues, follow these steps:
Sieve the clay body: to isolate some of the coarser particles.
Fire the sieved particles: to the same temperature as the bisque firing (body temperature).
Examine the fired particles: to see if any are active melters that decompose and release gases during firing.
Use a microscope: to examine pinholes in the glaze, looking for a glassy pool at the base of the pinhole.
If a glassy pool is present at the base of the pinholes, it suggests that the vigorous melting of coarse particles in the body, combined with the resulting glassy chemistry, is preventing the glaze from healing the pinholes.
In this case, the solution is to either:
Remove the problematic coarse particles from the clay body batch.
Grind the clay body more finely to reduce the size of the particles.
By eliminating or reducing the size of the active melting particles in the clay body, the gases released during firing will be distributed more evenly, allowing the glaze to heal any pinholes that form better.
Troublesome Materials in the Body?
If you notice white spots and dimples on the glaze surface after firing, it suggests that pinholes and other imperfections existed but have not fully healed. This may also indicate that the glaze melt does not flow as well as its glossy surface might suggest, implying that more flux or a later melting glaze might be needed.
Even clay bodies with fine particles can generate significant amounts of gas during firing, especially if they contain materials like talc, dolomite, or whiting that release high volumes of gas. It is common for potters to use a small amount of talc (2-5%) as a flux in mid-range clay bodies, but there are no practical and cost-effective alternatives that are as effective.
To adjust the glaze composition, firing schedule, and clay body materials, potters can minimize the appearance of white spots and dimples caused by incompletely healed pinholes in their glazed pottery.
Are There Soluble Salts in the Body?
If the bare-fired clay has a glassy film, it suggests that soluble salts within the body have migrated to the surface during drying. These soluble salts, if high in fluxing oxides, can act as a reactive intermediate layer between the glaze and the body. This reactive layer can exacerbate existing factors contributing to pinholing or create glaze surface irregularities similar to pinholing.
Add barium carbonate to the clay body mix to precipitate the soluble salts within the body. Substitute the implicated materials in the clay body batch with alternatives that do not contain high levels of soluble salts or fluxing oxides.
Is the Body Too Open?
The fired porosity of the clay body is a crucial factor in determining the quality of the final product. If the body has an open porous structure resulting from coarser particles, laminations, or air pockets (e.g., from poor pugging or the addition of sand, grog, shale, or unground clay), it can lead to issues during firing.
In a body that produces a significant amount of gases during firing, these gases escaping from within can be channeled into the porous network and converge at high-volume surface vents. If the gas volume is too large for the glaze to heal, it can result in defects like pinholes and blisters. Use a finer-particle body or apply a fine slip between the glaze and the body. This can help distribute the gases more evenly and prevent them from accumulating at specific points on the surface.
Is the Body’s Bisque Surface Rough or Irregular?
If the body surface is rough due to the presence of grog or sand, or if the ware has been mechanically trimmed during the leather hard stage, pinholes can often develop as the glaze dries on the body. This rough surface can lead to poor glaze lay-down, resulting in raw pinholes that may persist after firing. A rough surface exposes pore networks within the body to larger volume ‘exit vents,’ contributing to pinhole formation in glazes.
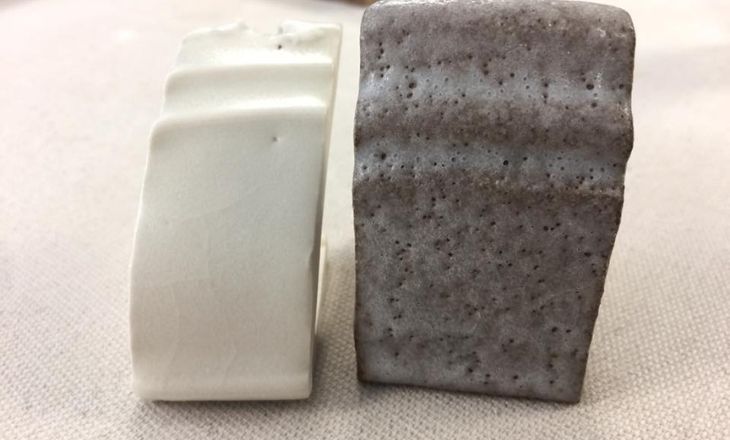
To prevent this issue:
- Use a finer body to reduce surface imperfections.
- Smooth the body surface in the leather hard state after trimming.
- Apply a fine-grained slip to create a smoother surface texture.
- Wash bisque ware (without soaking) before glazing to allow the wet glaze to fill surface irregularities and prevent air from being trapped in voids, which can lead to pinholes during firing.
Do You Understand the Gas Evolution Profile of the Body?
There are numerous methods available to analyze your body’s characteristics to help you regulate your breathing to slow down during periods of high gas evolution.
Do You Use Binders?
Glaze binders are recognized for causing significant issues like pinholing and pitting, with some decomposing at unexpectedly high temperatures. Consider switching to a binder that decomposes at a lower temperature, removing it if there is sufficient clay for the glaze layer to harden, or reformulating the glaze to melt faster using a fast-fire frit. It’s worth questioning the necessity of a binder and exploring if bentonite could serve the same purpose effectively.
Are Any Glaze Materials Contributing to the Problem?
Certain glaze materials, such as whiting, dolomite, talc, and coloring carbonates, can release significant amounts of gases as they decompose during firing, which can lead to issues like blistering if this decomposition occurs after the glaze has started to melt. Sources of the necessary oxides, like wollastonite for CaO and frits for MgO, can be used to reduce or eliminate these problems. Substitutions may require calculations to ensure the formula remains consistent.
Do You Need a Fast-Fire Glaze?
In the ceramics industry, there is a comprehensive understanding of the chemistry behind fast-fire glazes. These glazes typically contain zinc and lower boron, resulting in a delayed melting process. Failure to use a glaze specifically formulated for fast firing in such scenarios will likely lead to issues like glaze pitting and surface imperfections.
Is the Glaze Melt too Viscous?
If the glaze melt is overly thick, it can hinder flow, trapping gas bubbles within its structure. Viscosity in a glaze melt often indicates insufficient melting. Even well-melting glazes can resist flow due to factors like high alumina content or the presence of materials like Zirconium that stiffen the melt. Excessive melting leading to blisters or glaze boiling issues can be mitigated by adding Al2O3 to the formulation.
Is the Glaze Melting and Sealing the Surface Too Early?
Ideally, the body should release its gases before the glaze begins to melt. Modern fast-fire frits are designed to melt at a much later stage. The contemporary whiteware industry heavily relies on this concept, leading to a significant transformation in glaze formulations. Fusion frit 300 serves as a prime example of this innovation. If you are currently using early-melting high boron frits, consider reformulating your glaze to align with fast-fire formulations, even if you are not fast-firing.
Is There a Problem With the Glaze Application?
If the glaze layer is too thin, pinholes may result from a lack of sufficient glaze to heal them. Increasing the glaze thickness can significantly reduce the pinhole population, provided the glaze is stable enough to avoid running when applied thicker and fits the body well enough to prevent crazing due to increased tension between the two.
Improper application can also contribute to pinhole formation. Such pinholes are typically larger and may not be true pinholes, often accompanied by crawling. Ensure that the glaze slurry does not contain too much water, lays down into a dense layer on the body, and bonds well to produce a homogeneous dried surface with minimal airspace.
Is the Glaze Contaminated?
If pinholes are isolated and few in number, a contaminant getting into the glaze may be the cause. Pouring a sample through a fine screen can help check for this. Ball milling the glaze for an extended period, often up to 12 hours, can significantly improve fired surface qualities and resolve many pinholing and blistering issues. Many companies rely on this technique to achieve optimal results.
Is the Ware Once-Fire?
Once-fired ware is highly susceptible to crawling and pinholing due to the fragile glaze-body bond after application and the increased gas generation during firing compared to bisque-fired ware. While crawling is a common issue in once-fired glazed pieces, pinholes are more prevalent due to the significant outgassing during the initial firing process. The combination of these factors, especially with fast-fire techniques, can pose challenges in achieving a smooth-fired surface on a glaze.
Is There a Problem With the Glaze Firing?
If ware is fired too rapidly, the glaze melt may need more time to smooth over surface imperfections. Thicker or more protected sections of the ware often exhibit more pinholes, indicating that slower, more even firing can improve the surface quality across the entire piece. If the glaze does not pit or pinhole in sections opposite an unglazed surface, it suggests that body gases are the root cause, and the firing process needs to be adjusted at the appropriate time, or the body should use cleaner materials.
Modern automatic kiln firing devices make it convenient to control the firing curve. Serious pinholing problems have often been completely eliminated after studying the gas evolution characteristics of the body and glaze and employing a firing curve that slows down at appropriate times. Many industrial engineers specialize in the study of firing curves and the programming of automatic kilns.
Is There a Problem With the Bisque Firing?
To effectively address pinholes, it is advisable to bisque fire at a higher temperature and for a longer duration to eliminate the majority of gases during that firing process. Bisque at higher temperatures may reduce the ware’s absorbency, potentially making it less easy to glaze. Finding a suitable compromise temperature is essential. It is crucial not to stack ware too tightly during the bisque firing and ensure there is adequate airflow in the kiln to promote proper gas release.

Is the Problem Spit Out?
If the glaze surface displays numerous small broken blisters, the issue is likely due to spit-out, a phenomenon caused by the expulsion of trapped water vapor within porous ceramics during refire for luster decoration. It is remarkable how extended the process of driving off water can be during a fast firing, with water vapor potentially still being released past red heat. Ensuring that the ware placed in a glaze firing kiln is thoroughly dry is crucial to prevent such problems.
Conclusion
Glaze pinholing and pitting are common but manageable defects in ceramics that result from various factors such as improper application, inadequate firing schedules, and impurities in the glaze or clay body. By understanding the underlying causes, such as trapped gases, rapid firing, or incorrect glaze composition, potters can take proactive steps to mitigate these issues.
Adjusting the glaze formula, ensuring a clean and well-prepared clay surface, and implementing a controlled firing process are essential strategies for achieving smooth, defect-free glazes. Continuous experimentation and thorough documentation of processes and results will further aid in refining techniques and enhancing the quality of ceramic pieces.
FAQs
Are Pinholes in Glaze Food Safe?
Pinholes in the glaze can potentially make ceramics less food-safe. These tiny holes can trap food particles and bacteria, making thorough cleaning difficult and increasing the risk of contamination. Pinholes might indicate incomplete or improper glazing and firing, which could mean that the underlying clay body is not properly sealed, potentially leaching harmful substances into food. For food-safe ceramics, it’s crucial to ensure a smooth, fully vitrified glaze surface.
How to Fix Pinholes in Glaze?
To fix pinholes in glaze, you can try several methods. One option is to refire the piece at a slightly higher temperature or longer duration to allow the glaze to melt and fill in the pinholes. You can patch the pinholes by applying additional glaze with a small brush or spatula and then refiring the piece to blend it with the surrounding surface.
Another approach is to carefully sand the glazed surface to remove pinholes, although this method may alter the appearance of the piece. You can fill the pinholes with a thicker glaze mixture or spray a thin layer of glaze over them. Experiment with these methods to find the most effective solution for your specific situation.
What Causes Pinholes in Glaze?
Pinholes in glaze can be caused by various factors such as the presence of impurities in the glaze, inadequate preparation of the ceramic surface, improper firing schedules, or the release of gases during the firing process. These factors can result in the entrapment of air or other gases within the glaze, leading to the formation of small holes or pits on the glazed surface.