At What Temperature Can You Open a Pottery Kiln?
Pottery making is an ancient art form that requires patience, precision, and a deep understanding of the materials involved. One crucial aspect of the pottery process is firing the clay in a kiln to transform it into a durable work of art. But at what temperature can you open a pottery kiln? The answer lies in the delicate balance of temperature control and craftsmanship.
Opening a pottery kiln too soon can result in disaster – cracked pieces or even physical harm. The kiln has cooled to at least 125 F (51 C) before revealing your creation to the world. Understanding this critical step will not only protect your artwork but also elevate your pottery-making skills to new heights.
The High Heat Can Burn and Break Your Pottery
The high heat of a kiln is both a friend and a foe for pottery. While the intense temperatures are necessary for firing and strengthening the clay, they can also be the source of unexpected disasters. Inexperienced potters often fall victim to overheating their pieces, causing them to crack or even shatter under extreme conditions.
It’s crucial for pottery makers to understand the delicate balance required when working with high heat. A slight miscalculation in temperature or timing can result in irreparable damage to hours of work. Certain types of clay are more susceptible to breaking under excessive heat, adding another layer of complexity to the firing process.
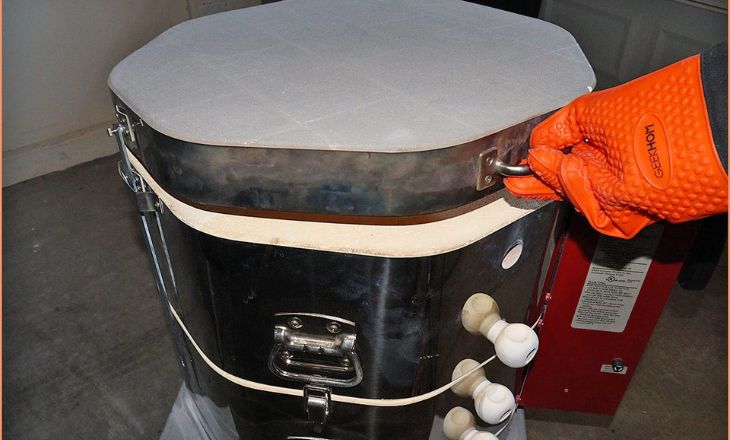
To prevent your hard work from going up in flames – quite literally – it is essential to closely monitor and regulate the kiln’s temperature throughout the firing process. Experimenting with different firing schedules and clay types can help you find the sweet spot where your pottery emerges unscathed from its fiery ordeal.
Letting Cool Air in Can Crack Your Pottery
When pottery is exposed to sudden changes in temperature, such as letting cool air in after firing, it can lead to cracks and fractures in the material. This phenomenon, known as thermal shock, occurs because different parts of the pottery expand and contract at different rates when subjected to drastic temperature variations. As a result, stresses build up within the object, causing it to crack.
To avoid this issue, potters use various techniques such as gradually cooling down the pottery or using specialized kilns that allow for controlled temperature changes. Selecting the right type of clay and glazes can also help minimize the risk of thermal shock during the firing process.
Can I Cool My Pottery Kiln Down Faster?
Yes, you can cool your pottery kiln down faster by using various techniques. One method is to prop open the kiln’s door slightly to allow heat to escape more quickly. Another option is to place fans around the kiln to help circulate air and expedite the cooling process. Additionally, some potters use a technique called quenching, where they carefully introduce water or other cooling agents into the kiln chamber to rapidly decrease the temperature.
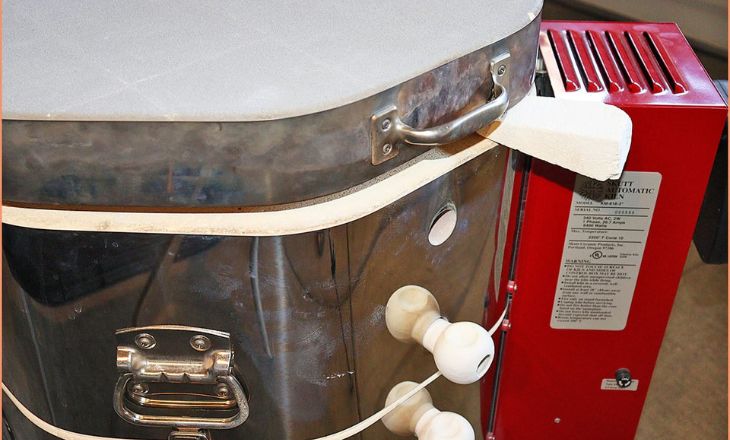
It’s important to note that cooling down a pottery kiln too quickly can lead to thermal shock and damage the pieces inside. Therefore, it’s crucial to follow proper guidelines and take precautions when attempting to speed up the cooling process. By experimenting with different methods and finding what works best for your specific kiln setup, you can effectively reduce cooling times without compromising the quality of your pottery pieces.
Does Having an Updraft or Downdraft Vented Kiln Matter?
One might wonder whether having an updraft or downdraft vented kiln truly matters in the firing process of ceramics. The design of a kiln can indeed have a significant impact on the results achieved. An updraft kiln allows heat and flames to rise naturally from the burning fuel to exit through the chimney, providing more even heat distribution throughout the kiln.
A downdraft-vented kiln pulls heat and flames down through the shelves before exiting out through the flue at the bottom. This type of kiln can help reduce hot spots and turbulence within the chamber, resulting in more consistent firings. The choice between an updraft or downdraft vented kiln ultimately depends on factors such as desired firing outcomes, ease of operation, and personal preference.
Factors That Affect How Quickly Your Kiln Cools
One crucial factor that affects the cooling rate of a kiln is its size and insulation. Larger kilns tend to cool more slowly than smaller ones due to the higher thermal mass that needs to be cooled down. Well-insulated kilns retain heat for longer periods, leading to a slower cooling process.
Another significant influence on how quickly a kiln cools is the firing temperature reached during the firing process. Kilns fired at high temperatures take longer to cool down compared to those fired at lower temperatures. This is because higher firing temperatures result in more intense heat retention within the kiln’s structure, requiring more time for it to dissipate completely.
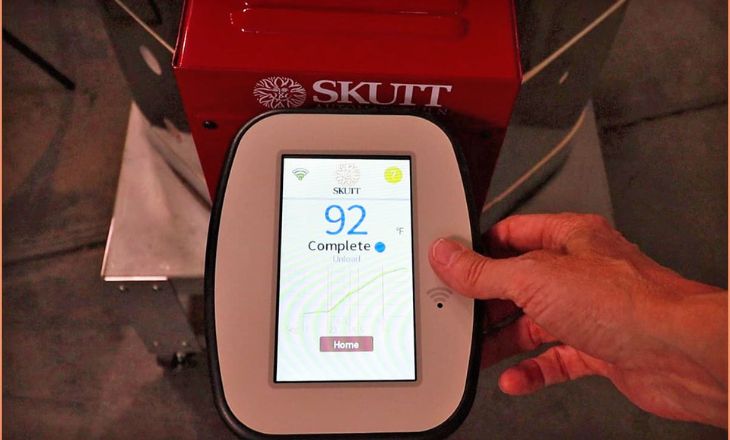
Environmental conditions such as ambient temperature and humidity also play a role in how quickly a kiln cools. In warmer climates or during humid weather, kilns may cool slower due to reduced temperature differentials between the inside and outside environments. Conversely, in colder or drier conditions, kilns are likely to cool faster as heat can disperse more rapidly.
The Style Of The Kiln
Factors that affect how quickly your kiln cools include the type of insulation used, the size and design of the kiln, and the ambient temperature of the environment. Kilns with thicker insulation tend to retain heat longer, resulting in slower cooling times. Smaller kilns cool faster than larger ones due to their lower thermal mass.
Another important factor is the design of the kiln itself. Kilns with efficient airflow systems can help speed up the cooling process by promoting better heat distribution and ventilation. On the other hand, poorly designed kilns may have hot spots or inadequate airflow, leading to uneven cooling and potential damage to your ceramics.
Ambient temperature plays a significant role in how quickly your kiln cools. In colder environments, it may take longer for a kiln to reach its desired temperature and consequently longer to cool down afterward. It’s important to consider these factors when planning your firing schedule to ensure successful results from your kiln firings.
The Level Of Insulation
The level of insulation in a kiln plays a significant role in how quickly it cools down after firing. Factors such as the thickness and quality of the insulation material can greatly impact the rate at which heat is retained or released. Inadequate insulation may result in rapid cooling, while excessive insulation could lead to slower cooling times, affecting the overall firing process.
The design and construction of the kiln also influence its insulating properties. A well-insulated kiln with proper sealing mechanisms can help maintain consistent temperatures during firing and ensure more controlled cooling rates.
The Size Of Your Kiln
The size of your kiln plays a crucial role in determining how quickly it cools down after firing pottery or ceramic pieces. Larger kilns tend to retain heat for a longer period due to their mass and volume, allowing them to cool at a slower rate compared to smaller kilns. This means that the size of your kiln directly impacts the cooling process, influencing the outcome of your fired creations.
Other factors such as insulation quality and ventilation also contribute to the cooling efficiency of a kiln. Proper insulation helps retain heat inside the kiln, while adequate ventilation promotes airflow and enhances cooling rates. By understanding these interconnected factors, potters and ceramic artists can optimize their kilns’ performance and achieve desired results consistently.
Choosing the right size for your kiln is essential for controlling the cooling process effectively. Consider factors like kiln dimensions, insulation quality, and ventilation when selecting a kiln size that aligns with your artistic needs and preferences. By paying attention to these details, you can enhance your firing experience and produce beautiful ceramic pieces with precision and efficiency.
Kiln Tips for Potters
One essential tip for potters when using a kiln is to ensure proper ventilation. Good airflow in the kiln helps prevent uneven firing and promotes even heat distribution, resulting in more consistent results. Consider adding vent holes or using a venting system to improve airflow during the firing process.
Another helpful tip is to carefully monitor the temperature in the kiln throughout the firing cycle. Use pyrometric cones or digital thermometers to accurately track the temperature and make adjustments as needed. Understanding how different temperatures affect your clay and glazes can significantly impact the final outcome of your pottery pieces.
Experiment with different stacking techniques inside the kiln to optimize space and ensure that each piece receives adequate heat exposure. By strategically arranging your pots, you can avoid hot spots and achieve more uniform results across all pieces in a single firing session.
Shared Kilns Will Cost Less To Operate
Shared kilns can offer a cost-effective solution for artists and hobbyists looking to fire their creations without breaking the bank. By sharing the kiln with others, you can split the operational costs, such as electricity and maintenance, making it more affordable for everyone involved. Sharing a kiln can also help in maximizing its usage, ensuring that it runs more frequently and efficiently.
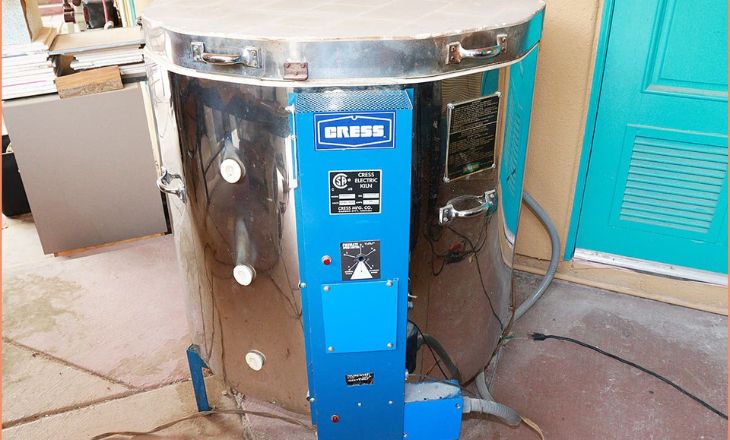
Shared kilns allow for a sense of community among users. Artists can exchange ideas, techniques, and even materials while utilizing the same resources. Overall, by opting for a shared kiln instead of owning one individually, users can save money while enjoying the benefits of communal art-making.
If You Know Buying a Pottery Kiln is Right for You
When considering purchasing a pottery kiln, it’s essential to factor in the associated costs. Kilns are not just a one-time expense but also require operational costs such as electricity and maintenance. The price range can vary significantly based on the size, style, and brand you choose. It’s crucial to set a budget and do thorough research to find a kiln that meets both your needs and financial capacity.
Beyond the monetary aspect, owning a pottery kiln also means working with fire and flammable materials. Safety should always be a top priority when setting up your kiln in an appropriate area with proper ventilation and fire protection measures in place. Understanding these considerations before diving into purchasing a kiln will ensure that you are fully prepared for the responsibilities and commitments that come with owning this valuable pottery tool.
Hire a Professional To Install Your Kiln
To install a kiln, hiring a professional is essential for ensuring a successful set-up. A skilled installer will have the expertise and knowledge needed to properly assemble and connect the kiln components. They can help troubleshoot any potential issues that may arise during the installation process, saving you time and frustration in the long run.
Professional installers also understand safety protocols and regulations surrounding kiln installations, reducing the risk of accidents or malfunctions. By entrusting this task to an experienced professional, you can have peace of mind knowing that your kiln will be installed correctly and efficiently. Overall, investing in professional installation services for your kiln is a wise decision that can lead to better performance and longevity for your equipment.
Conclusion
The temperature at which you can safely open a pottery kiln depends on the type of clay and glazes used, as well as the specific firing schedule followed. It is generally recommended to wait until the kiln has cooled down to around 200-300 degrees Fahrenheit before opening it to avoid any thermal shock to the ceramics inside.
Taking proper precautions and following manufacturer guidelines is crucial to ensure the safety of both the pottery and the artist. Remember, patience is key when dealing with high temperatures in pottery making – always prioritize safety over haste. Stay informed, stay safe, and happy firing.
FAQs
Can I Use An Oven Instead Of A Kiln?
An oven can be used for drying pottery but cannot reach the high temperatures required for proper firing, which typically exceed 900°C (1652°F). Proper vitrification and glaze maturation require a kiln.
Why Is My Pottery Cracking After Firing?
Pottery can crack after firing due to thermal shock, improper drying before firing, or issues with the clay body or glaze fit, such as differing rates of thermal expansion. Firing too quickly or unevenly can also cause cracking.
Can Pottery Be Glazed Without Firing?
No, pottery cannot be properly glazed without firing. Glaze needs to be fired to mature and fuse to the clay body, typically at temperatures above 900°C (1652°F), which cannot be achieved without a kiln.